Die Stampling for Metal badges coins
Metal stamping is a cold-forming procedure that takes advantage of dies as well as marking presses to change sheet metal into different forms. Pieces of level sheet steel, generally described as blanks, are fed right into a sheet steel marking press that utilizes a tool as well as die surface area to develop the steel into a new shape. Manufacturing centers and also metal makers offering marking services put the product to be stamped in between die areas, where making use of stress forms as well as shears the material into the preferred final form for the item or element.
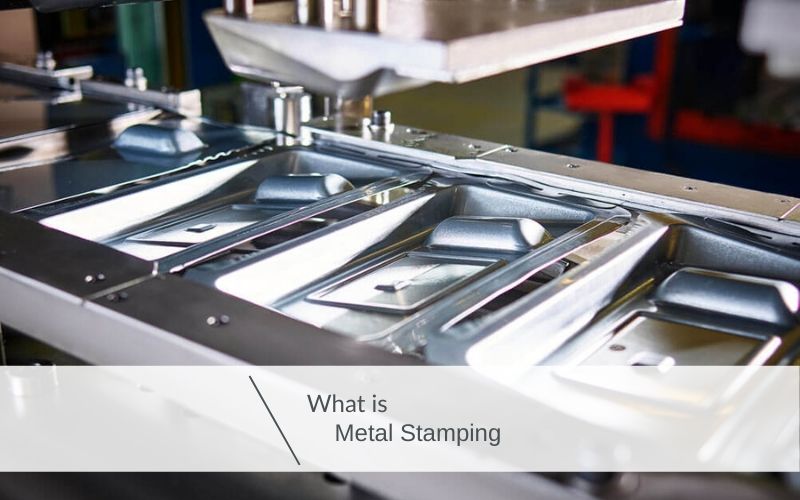
Fundamental Principles of Steel Stamping
Steel marking, additionally described as pressing, is a low-priced high-speed production process that can produce a high quantity of similar steel components. Stamping procedures are suitable for both short or lengthy manufacturing runs, can be carried out with various other steel developing procedures, as well as might comprise several of a collection of even more details processes or techniques, such as:
● Punching
● Blanking
● Embossing
● Coining
● Bending
● Flanging
Punching as well as blanking describe making use of a die to cut the material into specific forms. In punching procedures, a scrap piece of product is eliminated as the strike enters the die, properly leaving an opening in the workpiece. Blanking, on the other hand, gets rid of a work surface from the key material, making that removed part the desired workpiece or space.
Embossing is a procedure for producing either an increased or recessed layout in sheet steel, by pushing the raw blank versus a die which contains the wanted shape, or by passing the product blank through a roller pass away.
Coining is a flexing technique wherein the work surface is marked while positioned between a die as well as the strike or press. This action triggers the punch idea to pass through the steel and results in exact, repeatable bends. The deep infiltration additionally eliminates inner tensions in the steel workpiece, causing no bounce back results.
Flexing describes the basic technique of developing steel right into wanted forms such as L, U, or V-shaped accounts. The bending procedure for metal causes a plastic contortion which emphasizes over the yield factor however below the tensile toughness. Flexing usually occurs around a single axis.
Flanging is a process of presenting a flare or flange onto a metal work surface through the use of passes away, presses, or specialized flanging equipment.
Steel marking machines might do more than simply stamping; they can punch, cut and shape steel sheets. Makers can be set or computer system numerically regulated (CNC) to offer high accuracy as well as repeatability for every stamped item. Electric discharge machining (EDM) as well as computer-aided design (CAD) programs ensure precision. Numerous tooling equipments for the dies made use of in the stampings are offered. Progressive, developing, substance, as well as carbide tooling execute particular stamping demands. Modern dies can be used to create multiple items on a single item simultaneously.
Kinds Of Stamping Operations
Dynamic die stamping
Modern die stamping makes use of a sequence of marking terminals. A steel coil is fed into a reciprocating marking press with modern stamping passes away. The die moves with journalism, as well as when the press relocates down the die near to stamp the metal and also develop the part. When the press moves up, the steel moves flat along to the next terminal. These activities need to be precisely lined up as the component is still attached to the metal strip. The final terminal separates the newly-fabricated part from the remainder of the steel. Dynamic die stamping is ideal for futures, due to the fact that the passes away last long without obtaining damaged, and the procedure is extremely repeatable. Each step in the process carries out a various cut, bend, or punching procedure on the metal, thus slowly accomplishing the desired end-product form and layout. It is additionally a quicker procedure with a limited quantity of wasted scrap.
Transfer Pass Away Marking
Transfer die marking is similar to dynamic die stamping, yet the component is separated from the metal trip early at the same time as well as is transferred from one stamping station to the next by another mechanical transportation system, such as a conveyor belt. This process is usually used on majorities that might need to be transferred to various presses.
Kinds Of Stamping Presses
The 3 common kinds of marking presses consist of mechanical, hydraulic, as well as mechanical servo innovations. Typically, presses are linked to an automatic feeder that sends sheet metal with the press either in coil or empty kind.
Mechanical
Mechanical presses utilize a motor connected to a mechanical flywheel to transfer and store energy. Their punches can range in size from 5mm to 500mm, depending on the particular press. Mechanical pushing speed also varies, generally dropping in between the range of twenty and also 1,500 strokes per min, however they tend to be faster than hydraulic presses. These presses can be found in a range of dimensions that extend from twenty to 6,000 bunches. They are well-suited for producing shallower as well as easier parts from coils of sheet steel. They're usually utilized for progressive and transfer stamping with huge manufacturing runs.
Hydraulic
Hydraulic presses make use of pressurized hydraulic liquid to apply pressure to the material. Hydraulic pistons displace liquid with a force degree proportional to the size of the piston head, allowing for a postgraduate degree of control over the quantity of pressure, as well as a more regular pressure than a mechanical press. Furthermore, they include flexible stroke and also rate capabilities, as well as can usually deliver full power throughout any kind of point in the stroke. These presses generally differ in dimension from twenty to 10,000 tons and also use stroke dimensions from concerning 10mm to 800mm.
Hydraulic presses are normally utilized for smaller production runs to create much more challenging and also much deeper stampings than mechanical presses. They allow for even more versatility as a result of the flexible stroke length and regulated pressure.
Mechanical Servo
Mechanical servo presses make use of high capability motors rather than flywheels. They are utilized to develop much more complicated stampings at a faster rate than hydraulic presses. The stroke, slide placement as well as movement, as well as the rate are regulated and programmable. They are powered by either a link-assisted drive system or a direct drive system. These presses are one of the most expensive of the three types discussed.
Kinds Of Marking Passes Away
Passes away that are used in steel stamping procedures can be identified as either single-station or multiple-station dies.
Single-station dies consist of both compound dies and mix passes away. Compound dies perform greater than one reducing operation in a single press, such as the situation of the multiple cuts required to produce an easy washer from steel.
Mix dies are ones which include both reducing and non-cutting operations into a single press stroke. An instance may be a die that produces a cut in addition to a flange for a provided steel space.
Multi-station dies include both modern dies and transfer dies, where notching, punching, as well as reducing procedures take place in sequence from the same die-set.
The steel strip product made use of for the reducing surface area is developed to match the wanted form, and a slot is cut into the die footwear to hold the steel policy product. The features of the material to be cut, such as its density as well as solidity, assistance develop the steel rule thickness to be utilized in the reducing blade.
Material Factors to consider
The choice of metal stamping materials utilized depends upon the wanted features of the ended up item. Stamping is not limited as a manufacture process to simply metals - there are numerous products that can be refined with marking techniques, such as paper, leather, or rubber, however metals are without a doubt one of the most generally utilized.
Generally, steels often tend to maintain their pliability and ductility after stamping. Those used in precision marking usually range from soft to tool solidity and also bring a low coefficient of flow. Several of the customary steels and also steel types fabricated via stamping include:
● Precious metals, such as silver, gold, as well as platinum
● Ferrous metals, particularly iron-based alloys like stainless-steel
● Non-ferrous metals, such as bronze, brass, as well as zinc
● Non-standard alloys, such as beryllium nickel and also beryllium copper
Ferrous steels are generally utilized in marking procedures, as their low carbon content indicates they are among the least expensive alternatives readily available causing reduced unit production costs.
A number of crucial factors and also style factors to consider need to be addressed when carrying out metal marking procedures.
Completing Workflow
Post-stamping production procedures can consist of having the stamped product undergo deburring, touching, reaming, and also counterboring processes. These permit the addition of other components to be contributed to a stamped item or for the modification of blemishes in finish or removal of sharp edges that may influence security.
Deburring involves the elimination of fragments of cut product that stay on the work surface after the stamping procedure has been finished. Sharp edges may require grinding to remove burrs or might need to be flanged over to create a smoothed edge as well as to direct the burred side to the inside fold where it will certainly not create injuries or be noticed cosmetically.
Style Concepts
Overly narrow estimates must generally be avoided in stamped items, as these might be a lot more conveniently distorted and impact the understanding of top quality in the finished item.
Avoidance of sharp interior and also outside corners in stamped product layouts can help reduce the potential for the development of larger burrs in these locations as well as sharp sides that call for second therapy to remove. Likewise, a great possible for tension focus exists in sharp corners, which may trigger breaking or subsequent failure of the component with expanded usage.
General dimensions for the ended up product are going to be limited by the available dimensions of the sheet steel sheets or spaces, and also these limitations need to be factored for the product eaten in folds up on edges or flanges and also any type of added material elimination or use. Very large items may require to be developed in multiple steps and also mechanically collaborated as a second action in the manufacturing procedure.
For punching operations, consider both the instructions of punching as well as the dimension of the punched function. Usually, it is best to do punching in one direction, to ensure that any kind of sharp edges produced by the strike will certainly all get on the very same side of the workpiece. These edges can after that be hidden for appearance functions and also kept away from basic gain access to by workers or product end-users where they may stand for a danger. Punched attributes should mirror the density of the raw material. A general regulation is that punched functions must be at the very least two times the product density in dimension.
For bends, the minimum bend radius in sheet steel is approximately the same as the material density. Smaller sized bends are more difficult to attain and might cause factors of stress focus in the completed component that might ultimately cause concerns with product quality.
When exploration or punching openings, performing these procedures in the same step will assist to guarantee their positioning, resistance, and also repeatability. As general guidelines, opening diameters need to be no smaller sized than the product density, and the minimal spacing of holes should go to least twice the material density apart from each other.
Bending procedures need to be executed with recognition of the threat or distorting the material, as the product on the interior and exterior surface areas of the bend factor are pressed and also extended specifically. The minimal bend distance ought to be roughly equal to the thickness of the work surface, once again to stay clear of anxiety focus accumulate. Flange sizes ought to be more like 3 times the workpiece density as a good technique.
Marking Advantages
Several of the advantages of marking consist of lower die expenses, reduced second costs, and also a high level of automation compared to other procedures. Metal marking passes away often tend to be relatively less costly to create as well as preserve than those used in various other common procedures. Marking equipments are fairly easy to automate and also can utilize high-end computer-control programs that offer higher accuracy, quicker manufacturing, and also quicker turnaround times.